sheet metal forming In this article, learn the basics of sheet metals, the various sheet metal forming processes, and how to reduce the cost of sheet metal forming with rapid tooling and 3D printed dies. For a . Cold and hot rolled steel: 16 gauge, 14 gauge, 1/8" and 1/4". Copper: 48 oz, 24 oz, 20 oz and 16 oz. Galvanized steel: 24 gauge, 20 gauge, 18 gauge and 16 gauge.
0 · sheet metal layout drawings
1 · sheet metal forming types
2 · sheet metal forming process pdf
3 · sheet metal forming press dies
4 · sheet metal forming pdf
5 · forming sheet metal by hand
6 · forming process in sheet metal
7 · bulk deformation vs sheet metal forming
Some call them 'anti-rattle clips or retention clips. They keep your pads within a certain tolerance of variance regarding the touch points on the disk. As well, they prevent the pads from rattling as you drive down the road and the pucks within your calipers are retracted just a .
Also known as sheet metal fabrication, sheet metal forming uses metal sheets to make various products and components. The metal sheets are formed and cut into the necessary shape and size via many different . Sheet metalworking, also known as Sheet metal forming and sheet metal fabrication, is a manufacturing process of cutting and forming relatively thin metal sheets, strips, and coils to create desired shape sheet .In this article, learn the basics of sheet metals, the various sheet metal forming processes, and how to reduce the cost of sheet metal forming with rapid tooling and 3D printed dies. For a . Learn the basics of sheet metal forming, a process of shaping flat metal into three-dimensional objects. Find out the types of sheet metal, forming techniques, tools, safety precautions, and challenges involved.
Learn how to transform flat sheets of metal into various parts with intricate shapes using different techniques such as bending, curling, ironing, hydroforming and punching. Discover the best practices for material selection, .
%PDF-1.4 %âãÏÓ 663 0 obj > endobj 685 0 obj >/Filter/FlateDecode/ID[704E8A5A77AA90E0E45753C1AAABDACC>]/Index[663 39]/Info 662 0 R/Length 112/Prev 3172114/Root 664 . Sheet metal forming involves several key techniques and processes, each tailored to specific applications and desired outcomes. These include: 1. Bending. Bending is a fundamental sheet metal forming process .Sheet metal expanding is a specialized process within sheet metal forming that involves stretching the metal to create a mesh-like pattern. This technique enhances the flexibility and strength of the sheet metal, making it suitable for various applications, including filtration, screening, and architectural details.From metal cans to protective housing for hardware, parts created by sheet metal forming are found everywhere in our daily lives. In this article, learn the basics of sheet metals, the various sheet metal forming processes, and how to reduce the cost of sheet metal forming with rapid tooling and 3D printed dies.
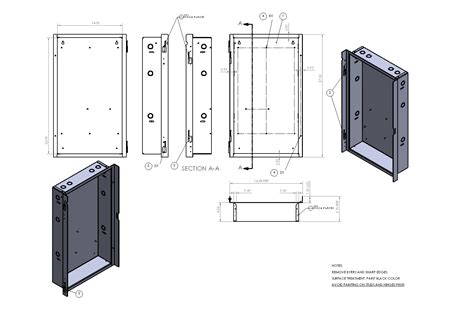
Sheet metal forming involves a process known as curling, in which sheet metal components are given smooth edges and cylindrical shapes by eliminating sharp edges or burrs. Curving provides extra safety due to its ability of getting rid of rugged areas that could be potentially dangerous during handling or use. There is a wide range of tools .Incremental sheet forming or ISF forming process is basically sheet metal working or sheet metal forming process. In this case, sheet is formed into final shape by a series of processes in which small incremental deformation can be done in each series. Ironing Ironing is a sheet metal working or sheet metal forming process. . In this video we will discuss three basics to sheet metal forming. For more information visit www.rapidmanufacturing.comThe best in sheet metal forming equipment, along with highly skilled software technicians and experienced metal forming fabricators allow us to move your parts from order to completion in days. And WE GUARANTEE IT! You’ll receive 0 off your order if you don’t get a same day quote with 6-day turn around and shipped within 7-days.
acrylic letter cnc cutting machine suppliers
Sheet metal forming involves a wide range of processes that manufacture parts for a vast amount of purposes, both seen and unseen. Sheet metal refers to metal that has a high surface area to volume ratio. Sheet metal work stock, used for sheet metal processes, is usually formed by rolling and comes in coils. .Traditional sheet metal forming is a capital- and time-intensive process that requires an expensive stamping press, which often costs about million, as well as tools and dies that take months to produce. While similar processes such as hydroforming, fluid cell presses, and zinc low-cost die tooling aim to reduce the time of forming sheet .Sheet Metal Forming. Application ID: 11208. This example benchmarks a NAFEMS validation model of a friction contact problem with an elastoplastic material model. A thin metal sheet is forced into a die by a punch. Both the compressing displacement and the release of the punch are modeled in order to compute the forming angle (at the maximum .
Our facility houses four press brakes that allow us to offer a wide range of sheet metal forming capabilities. While all of our press brakes help us complete projects, two of them deserve a special mention. First, our high-speed electric press brake allows us to work with more accuracy and efficiency. It’s faster and includes added safety .Validate Metal Sheet Forming with a Single Tool. Ansys Forming simulates all metal stamping tasks through an end-to-end workflow that allows you to perform the entire die process in a single platform, with the fastest solve time.Air-Powered Sheet Metal Forming Hammers. These air-powered tools remove dents, smooth out ridges, and shape sheet metal more efficiently than manual hammers. Forming Spoons. Place against the face of your workpiece and strike with a hammer. The blow will transfer to the workpiece without damaging the finish.
Desktop Metal, Inc. (NYSE: DM) introduces the Figur G15, the first commercial platform of its kind to shape standard sheet metal on demand directly from a di.
What is metal forming? Metal forming processes are used to apply stress, compression, or both upon a piece of metal. . process. It typically utilizes a brake press, but can also be performed by similar press machines. In this process, a . Sheet Metal Forming and Slide Forming Department Valco Valley Tool & Die is your global source for metal parts manufacturing in Cleveland, Ohio. Recognized for our upstanding reputation for quality products, services, and .Opening the Model and Inserting a Forming Tool. Next, you open a sheet metal part and add the formed louver from the Design Library. Specifying the Louvers. Next, you specify the louver rotation angle and insert two more identical louvers. Replacing Forming Tools. Next, you replace the louver forming tool with an extruded hole forming tool. Support these projects on patreon: https://patreon.com/stuffmadehereCheck out the subreddit: https://tinyurl.com/smhereIn this video I show more techniques f.
Sheet metal forming can bend the part in multiple directions, creating simple parts such as brackets up to highly complex geometries which may require custom die tools. Once the tools are in place, making subsequent sheet parts in production is very cost-effective. This makes sheet metal fabrication and forming ideal for low to high volume . One of the key advantages of sheet metal hydroforming is its ability to produce parts with reduced material waste and cost savings compared to traditional forming methods. The process allows for the use of thinner materials while still maintaining the required strength, which can result in lighter parts and lower production costs.Developments in the numerical modeling of stamping processes and experimental measurements now make it possible to design stamping processes using sound engineering principles. This article shows how experimental and theoretical contributions have led to the concept of a forming window in strain space that identifies the strains that can be developed safely in a sheet .
sheet metal layout drawings
sheet metal forming types
Sheet metal forming processes are those in which force is applied to a piece of sheet metal to modify its geometry rather than remove any material. The applied force stresses the metal beyond its yield strength, causing the material to plastically deform, but not to fail. By doing so, the sheet can be bent or stretched into a variety of complex shapes.Our sheet metal forming capabilities include precision metal bending, metal rolling, and structural steel rolling; including: angle, tube, beam, and more. From simple metal brackets and signboards to complex metal components, we specialize in offering press brake forming services for a wide range of sheet metal fabrications. Sheet metal forming covers a variety of processes wherein shearing, bending, stretching, and drawing or their combinations are used to produce parts for a wide variety of applications. Most of the conventional sheet metal forming operations require component-specific and costly tooling, and their design and fabrication add to the lead time.
Deep drawing is a sheet metal forming technique in which a sheet metal blank is mechanically dragged radially into a forming die by the action of a punch. As a result, the process is a sharp transformation with material retention. When the depth of the drawn component exceeds its diameter, the technique is referred to as "deep drawing" Coming to the sheet metal forming processes itself, drawing and bending are the two most widely used techniques in sheet metal industry. Both experimental and FE based simulation works have been done in analyzing these two processes. It is understood from the literature that punch nose radius and die shoulder radius coupled with appropriate .
add outlet outside junction box
Known as star bolts or star anchors, they're not strictly decorative. Instead, the star is the washer for an iron rod placed through a sagging or compromised wall to preserve.
sheet metal forming|forming process in sheet metal